Since our establishment in 1924,MERZEN PRODUCTS has been dedicated to the design and development of fastening solutions,
including safety pins, clips, and name tag parts. We also specialize in OEM/ODM services,
collaborating with customer brands to design and manufacture custom fasteners that are widely adopted across various industries.
From planning and development to manufacturing, we handle all processes in-house to ensure consistency and quality.
With 'fastening' as our guiding principle, we are committed to maintaining the reputation of "MADE IN JAPAN" through our craftsmanship.

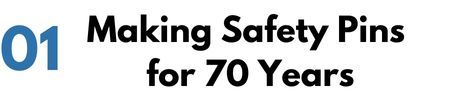
MADE IN JAPAN: The Craftsmanship
The production of safety pins began in Nagoya after World War II.
In 1957, we initiated research towards the automation of safety pin manufacturing.
After several years of dedication, we succeeded in achieving stable quality from production to plating,enabling large-scale production.
Today, our products are widely utilized as fasteners for name tags, can badges,
and tag attachments for cleaning purposes across various industries.
They were also utilized as bib fasteners in various events during the 2021 Tokyo Olympic Games.We continue to manufacture these products at our factories in Aichi and Gifu prefectures in Japan.
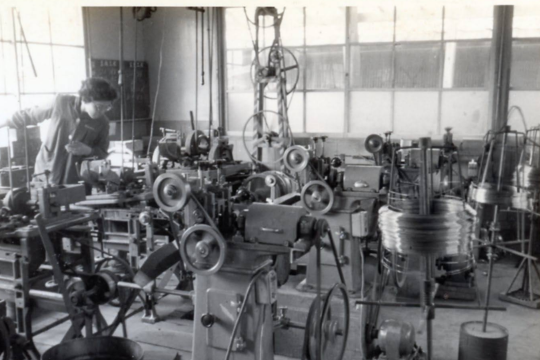
Precision Needle Points and Plating
The needle points of various pins are crafted through in-house polishing by our artisans.
The tip of the needle is bullet-shaped, ensuring smooth passage through fabric while also providing resilience against bendingand breakage.
Additionally, our plating process involves the installation of dedicated lines within our facilities.We ensure proper plating coverage up to the needle points and adjust according to manufacturing date temperatures and humidity levels,
ensuring a high-quality, rust-resistant finish
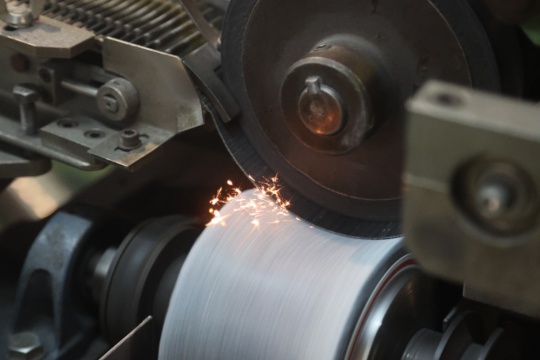
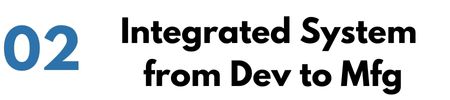
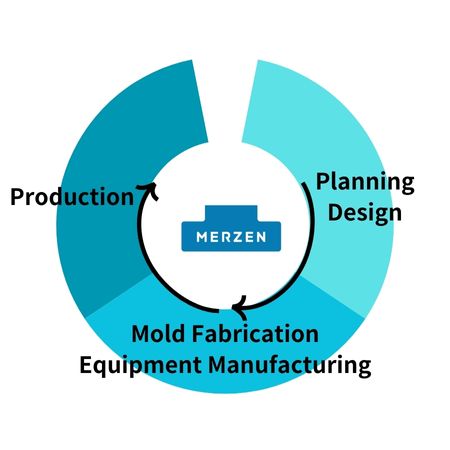
In-House Integrated Production
We achieve in-house integrated production by developing everything from planning and design to manufacturing,
and even manufacturing equipment if necessary, within our company.
By conducting all processes in-house, we realize accelerated development speed and rigorous quality control
from the inception of product development. This enables us to establish a system for consistently supplying high-quality products.
From Spring to Design & Manufacturing
Currently, we manufacture several hundred types of clips. Each one of them utilizes designs developed in-house from the spring,
ensuring they are tailored to specific purposes and applications, achieving optimal "gripping power" and "firmness".
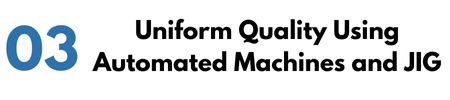
Striving for the Balance of
"Reliable Quality" and "Low Cost"
In pursuit of both "reliable quality" and "low cost," many of the clips we manufacture, including safety pins, are produced in-house from resin components to springs. We utilize our own manufacturing facilities for assembly. Additionally, for products requiring assembly such as various types of clips, we create fixtures for each product. This allows us to ensure a certain level of quality during manual assembly, thereby establishing a system that guarantees both "reliable quality made in Japan" and "low cost".
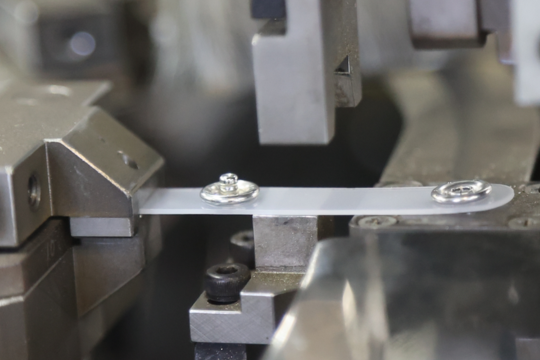
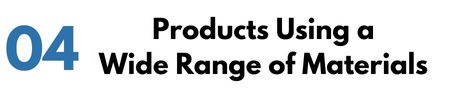
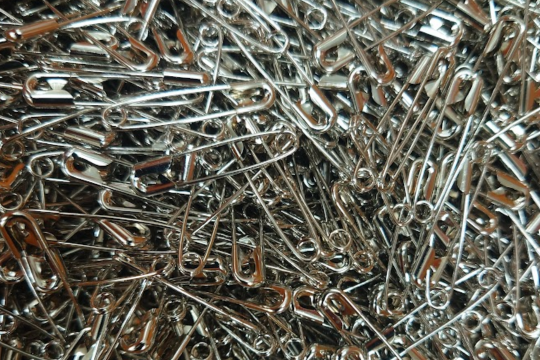
Material Selection According to Purpose
We specialize in both metal and plastic products. Our journey began with the production of safety pins after world war II. Initially, our products were made solely from iron, but in response to various applications and customer demands, we expanded our expertise to include stainless steel and brass, acquiring metal processing and manufacturing techniques. Furthermore, our plating technology, conducted in-house, has been diversified to accommodate different materials and purposes.
In our product lineup, we offer a range of products for clips, including both metal and plastic types for casings and springs, allowing customers to choose according to their needs. Recently, we have been actively conducting prototype research using various bioplastics, promoting environmental sustainability both internally and externally.
。
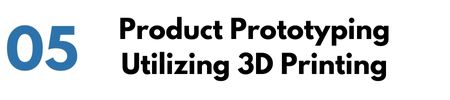
Improving Development Speed
By utilizing 3D printers, we promptly materialize ideas and conduct product image confirmation within our company or with customers, facilitating mold making. Additionally, by grasping aspects such as the "click" sensation when fastening that cannot be conveyed through drawings before mold making, we minimize corrections during mold making, achieving short lead times and cost reductions.
Mitigating Security Risks
By owning 3D printers in-house, we contribute to preventing information leakage by eliminating the need for external data sharing, even when visualizing shapes in the design stage.
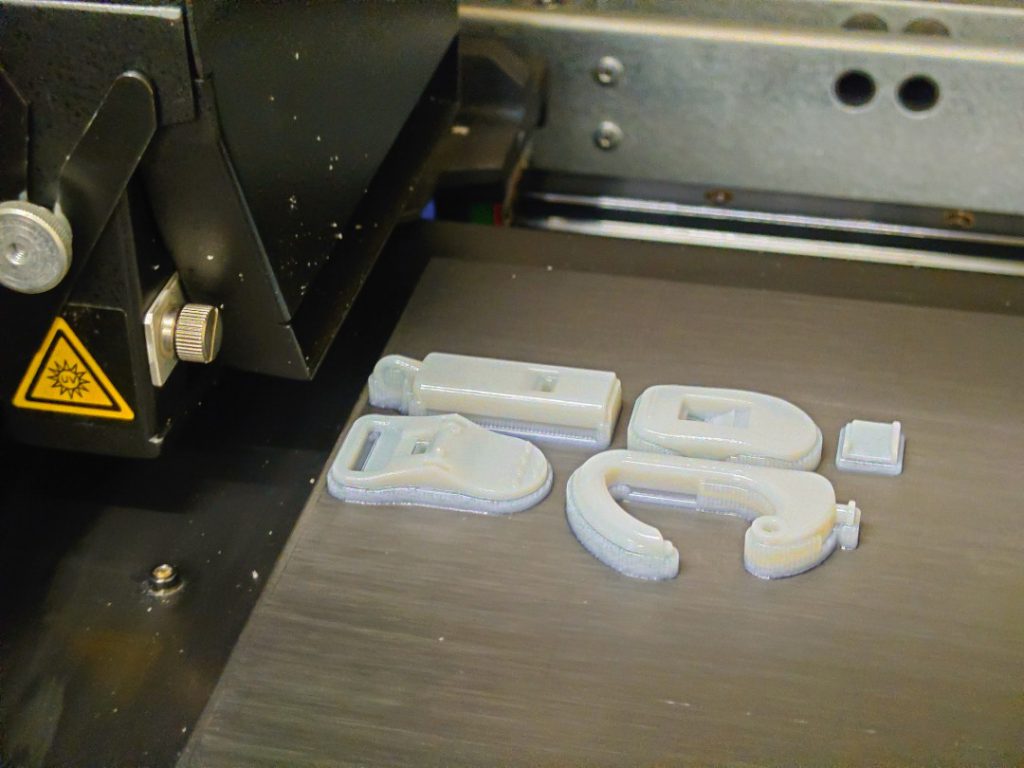
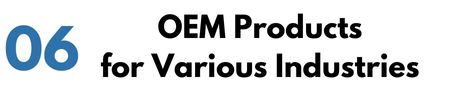
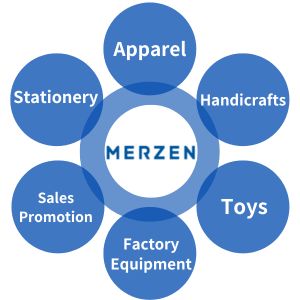
We have been walking alongside customers from various industries such as stationery and apparel as an OEM/ODM manufacturer, aiming to create original products with "fastening" as the keyword and solve our customers' fastening-related challenges. Putting delivering highly functional and high-quality fasteners full of originality to our customers as our top priority, we will continue to challenge ourselves in product development, production, and quality control.
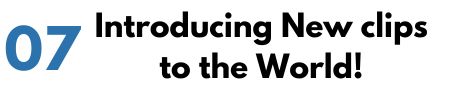
Have you ever come across these products somewhere?
In Japan, these products are widely used in various situations.
Band clip is used for name tags and pocket pouches.
CLIX is used for signage in stores, offices, and factories.
Fish Clip is used for preventing blankets or hats from falling.
These are all products that we have developed and created.
We have shaped each of them according to the changes in society and the times, meeting the needs of each moment.
We will continue to create new products that do not yet exist and connect them to the next 100 years.
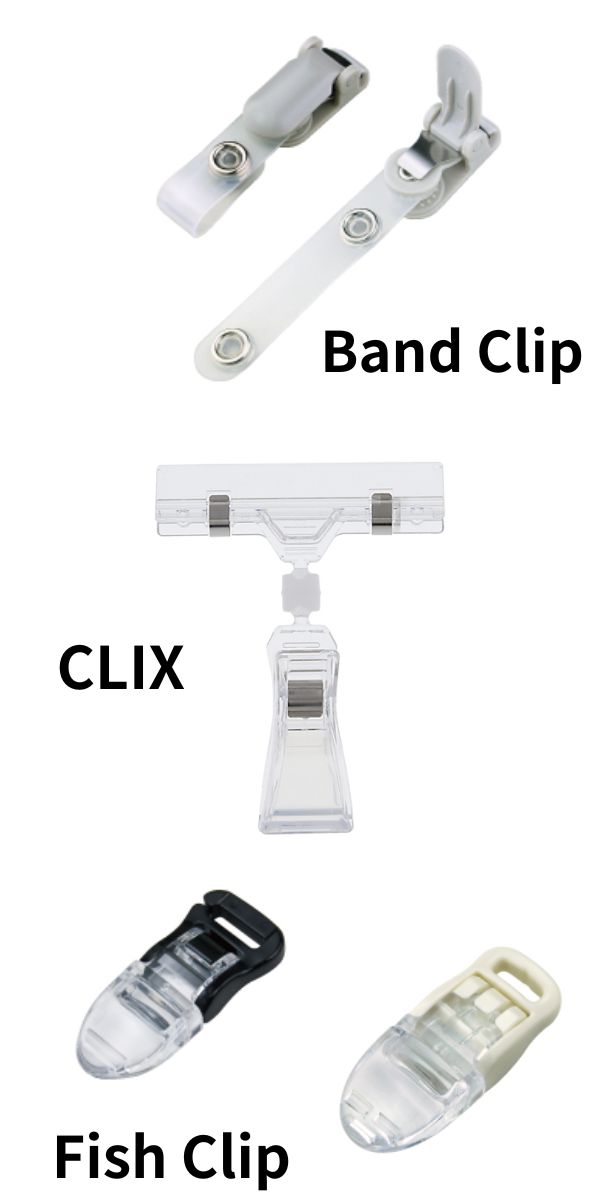